Table of Contents
Resumen
Con la ayuda del escáner dental DS300 de SHINING 3D, mediante la aplicación del software Exocad y bajo la dirección del técnico español Waldo Zarco Nosti, un laboratorio dental de Shenzhen logró con éxito la fabricación de prótesis de implante de mandíbula edéntula completa mediante el proceso de restauración dental digital.
I. Modo de escaneo dental
Durante la etapa de preparación, el técnico dental del laboratorio dental utilizó 6 cuerpos de escaneo, y los fijó en análogos dentro del modelo de yeso con un destornillador. La gingiva artificial del modelo se retiraba para comprobar si las piezas de conexión estaban colocadas o no.
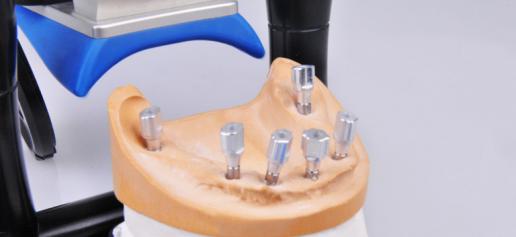
Cuando se realizó el paso de escaneado con cuerpos de escaneado, se retiró la encía artificial para asegurarse de que los cuerpos de escaneado se colocaban completamente.
Una vez finalizados los trabajos preparatorios, se escanearon sucesivamente los modelos de oclusión superior e inferior, el modelo de mandíbula, el modelo de trabajo con encía artificial y el modelo de trabajo con cuerpos de escaneado utilizando el escáner DS300 de SHINING 3D bajo la guía de su software de escaneado 3D autoequipado DentalScan. Cuando se escanearon los modelos de oclusión superior e inferior, se utilizó un accesorio oclusal especial equipado para el DS300. Los puntos marcados en el accesorio oclusal podían utilizarse para identificar la posición espacial del modelo, transfiriendo así la relación posicional al software de diseño CAD.
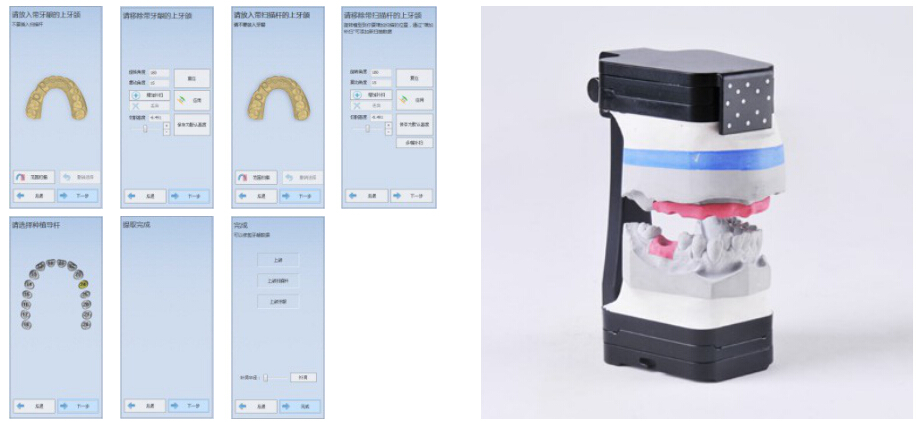
El usuario realiza la operación de escaneado siguiendo las indicaciones del software de escaneado DentalScan de SHINING 3D.
Cuando se escanean los modelos del maxilar superior e inferior, la herramienta de transferencia de oclusión equipada para el DS300 puede fijar los modelos del maxilar superior e inferior. Los puntos marcados en ellos se utilizan para lograr la posición de transferencia durante el proceso de escaneado.
II. Modelado de software
Una vez obtenidos los datos del escaneado 3D, el técnico español Waldo Zarco Nosti diseñó la prótesis utilizando Exocad. Dentro del software de diseño, el técnico seleccionó los cuerpos de escaneo de los datos CAD correspondientes al tamaño de la plataforma de los datos del implante y los alineó con la sección de cuerpos de escaneo de los datos de escaneo sucesivamente para lograr la mejor coincidencia. Este paso de alineación es extremadamente crítico, porque determinaría directamente si la estructura superior podría lograr un “ajuste pasivo”.
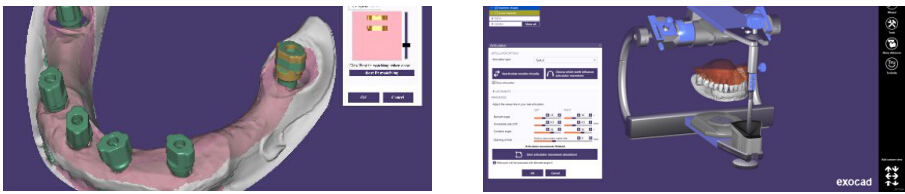
La función de ajuste óptimo de exocad puede obtener el mejor resultado utilizando los datos CAD de los cuerpos escaneados en la base de datos para alinearlos con los datos escaneados.
Como se utilizó la herramienta especial de transferencia de la relación de mordida del escáner DS300, la relación espacial entre los modelos del maxilar superior e inferior y el articulador dental se transfirió completamente al articulador virtual dentro del software de diseño.
Dado que se utilizó el accesorio oclusal especial del escáner DS300, el articulador virtual Amann Girrbach® pudo abrirse directamente dentro del software de diseño exocad, y la posición del modelo digital dentro del articulador virtual fue completamente consistente con la posición del modelo de yeso dentro del articulador físico Amann Girrbach®. Por lo tanto, el movimiento oclusal podía simularse completamente dentro del software para eliminar las intersecciones que pudieran aparecer en la prótesis durante el movimiento.
El movimiento oclusal es simulado por el articulador virtual en el software. Las intersecciones en la prótesis pueden visualizarse y eliminarse directamente para evitar un contacto prematuro en la prótesis terminada.
Basándose en la forma anatómica completa del paso anterior, el modelo se recorta en la estructura basal. Las ranuras de retención mesial-distal se preparan con una herramienta de tallado.
En los procesos, el puente basal se diseñó utilizando las ubicaciones de las ranuras de retención mesial-distal.
III. Fabricación de la prótesis
Una vez terminado el diseño del puente basal, se fresó el puente metálico con una fresadora de cinco ejes. El puente se ajustó muy bien al modelo gracias a muchos factores, entre los cuales, sin embargo, fueron esenciales los datos de alta calidad adquiridos por la cámara de alto píxel del DS300.
Tras el procesado, se completó el recubrimiento de acabado con resina fotopolimerizable y se llevó a cabo la reparación estética de las zonas rojiblancas para obtener muy buenos resultados.
El soporte metálico procesado se ajusta completamente al modelo sin inclinarse cuando se prueba. El acabado se ha realizado con resina fotopolimerizable.
Esta figura muestra otro ejemplo de cierre de barra acabado con DS300, en el que todas las piezas de conexión encajan muy bien.